智能化物流系統(tǒng)可以極大降低物流和倉儲成本。智能化物流系統(tǒng)達到了較高的自動化控制程度,減少了物料流轉過程中的手工操作,從而很大程度上避免了由于人員操作失誤而導致的損壞和丟失,降低了物流過程中的損耗。此外,智能化物流系統(tǒng)能與供應商的供貨系統(tǒng)對接,實現零庫存管理,最小化倉儲成本。
智能化物流系統(tǒng)能夠協助企業(yè)提升生產和倉儲效率。智能化物流系統(tǒng)能夠幫助企業(yè)真正實現倉庫與車間的聯動,從而確保在正確的時間、正確的地點讓正確的用戶獲得正確數量的正確物料。這樣可避免生產線上物料不足或者物料積壓造成的生產效率下降。同時,智能化物流系統(tǒng)能夠幫助制藥企業(yè)基于實時數據合理高效地使用倉儲設施,提升整體物流效率。
智能化物流系統(tǒng)是制藥企業(yè)實現全過程可追溯性的重要環(huán)節(jié)。系統(tǒng)可基于統(tǒng)一的編碼規(guī)則實現物料識別,對物料的接收、入庫、出庫、退回,以及半成品、成品的生產、流轉進行實時監(jiān)控和追蹤,以實現物流系統(tǒng)中的可追溯性。通過在企業(yè)內部建立統(tǒng)一的編碼規(guī)則,可以進一步實現物料和產品在制藥企業(yè)全操作流程中的可追溯性。
此外,智能化物流系統(tǒng)還能夠幫助企業(yè)降低質量風險。智能化物流管理系統(tǒng)以統(tǒng)一的編碼規(guī)則為前提,在物料收貨、上下架、配送和退庫操作中實現精確管控,防止物料的污染和交叉污染,避免了由于投料錯誤引發(fā)產品質量問題。
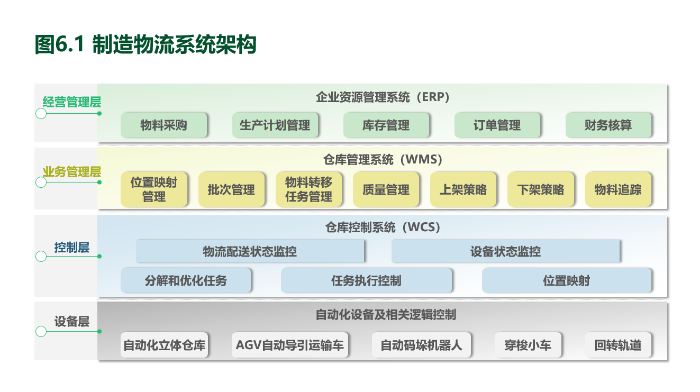
系統(tǒng)架構
企業(yè)可在制造物流計算機系統(tǒng)架構設計上,參照企業(yè)系統(tǒng)與控制系統(tǒng)集成國際標準ISA-95結構模型,借助該模型實現不同系統(tǒng)之間的集成,達到數據整合、信息共享的目的,實現企業(yè)內外全業(yè)務、全流程的互聯互通。
該結構模型包含四個維度。設備層包括現場自動化設備及相關邏輯控制。制造物流系統(tǒng)中常見的自動化設備包括自動化立體倉庫、AGV自動導引運輸車、自動碼垛機器人、穿梭小車、回轉軌道等。這些自動化設備及其邏輯控制系統(tǒng)通過與控制層的倉庫控制系統(tǒng)通信,實現接收任務、執(zhí)行任務、發(fā)送確認等功能。
控制層為倉庫控制系統(tǒng)(WCS),是介于倉庫管理系統(tǒng)和各類自動化設備之間的控制系統(tǒng),用于協調運行各種自動化物流設備(如自動導引運輸車、自動碼垛機器人、回轉軌道)。通過分解和優(yōu)化任務、分析執(zhí)行路徑,為上層系統(tǒng)的調度指令提供執(zhí)行保障并進行優(yōu)化,實現對各種設備系統(tǒng)接口的集成、統(tǒng)一調度和監(jiān)控。
業(yè)務管理層為倉庫管理系統(tǒng)(WMS)。該系統(tǒng)綜合了位置映射管理、批次管理、物料轉移任務管理、質量管理、上架策略、下架策略、物料追蹤等功能,控制并跟蹤物流管理全過程,并及時、準確地采集任務完成的結果及各個階段產生的物流數據,從而實現實體庫位信息與系統(tǒng)的一致,保證物料流轉信息的可追溯性。此外,該系統(tǒng)還可以和制造執(zhí)行系統(tǒng)等其他系統(tǒng)集成,實現物料的自動調配。
經營管理層為企業(yè)資源管理系統(tǒng)(ERP),具有物料采購、生產計劃管理、庫存管理、訂單管理、財務核算等功能。收貨、下賬等涉及生產物料總數量、總價值的內容通常通過ERP系統(tǒng)進行管理。
制造物流管理包含物料管理和倉儲管理兩個部分。物料和倉儲管理智能化可極大提升物料配送的速度和精度,改善倉儲空間利用效率,提高信息獲取的及時性和準確性。同時,還可削減人工成本,降低物流損耗,提高整體效率。
物料管理
智能化物流管理可極大優(yōu)化物料管理各環(huán)節(jié),實現從接收、質量檢驗、生產物料發(fā)送、成品和半成品入庫以及剩余物料退回的全流程監(jiān)控和數據搜集。
物料的接收是生產制造企業(yè)物流系統(tǒng)的開端,它的核心在于對接收的物料進行數字化標識。企業(yè)可基于RFID等數字化標識來標記物料,并將已接收的物料名稱、批號及數量信息與托盤或專用容器綁定。通常托盤或專用容器也應有可自動識別的唯一設備編碼。
物料檢驗的第一步是在其上架前由系統(tǒng)自動進行外形檢測。具體步驟為,系統(tǒng)讀取物料的信息化標識,對檢測結果顯示為超高、超長、超寬、超重或信息無法識別的物料自動剔除,以保證物料符合軌道運輸和貨架保存的物理要求。接下來,可根據物料的實際物理參數和物料標識信息自動分配至對應存儲區(qū)域的貨位,并保證物料在運輸過程中的有效追蹤。收貨系統(tǒng)可進一步與實驗室管理系統(tǒng)集成,在收貨后自動觸發(fā)檢驗任務,提醒質量控制部門進行取樣檢驗,并在檢驗后在倉庫管理系統(tǒng)中更新物料質量狀態(tài)。
將生產物料發(fā)送到車間進入生產流程的最基本要求是準確和及時。一方面,需滿足GMP對物料管理的要求。應保證倉庫管理系統(tǒng)能夠監(jiān)控庫存物料的質量狀態(tài),只允許質量狀態(tài)顯示為可用的物料發(fā)送至生產區(qū)域。另一方面,需推動生產效率的提高??苫谥圃靾?zhí)行系統(tǒng)或自動看板系統(tǒng)的物料需求,通過拉動的方式,由庫房管理系統(tǒng)按需配送物料至目標區(qū)域,從而減少生產線上出現物料積壓情況,使得物料周轉更加高效、順暢。倉庫管理系統(tǒng)可根據需求配置物料的下架策略(如后進先出、先進先出),以管理庫存中物料發(fā)料時的出庫順序。
成品、半成品生產完成后由系統(tǒng)自動生成可識別的數字化標識,自動在系統(tǒng)中完成物料接收、庫存創(chuàng)建與控制、實物位置及質量狀態(tài)跟蹤。成品箱碼垛工作可由自動化設備完成,例如使用中央碼垛系統(tǒng)對成品箱進行碼垛,設備完成碼垛后自動執(zhí)行上架入庫指令,減少人工操作,避免人為差錯,同時提高空間利用率。
生產結束后的剩余物料如需退回至倉庫,可在制造執(zhí)行系統(tǒng)中進行退料操作。倉庫管理系統(tǒng)可自動更新物料的批號、數量、位置等信息,自動創(chuàng)建取貨任務,并通過外形檢測和信息識別保證退回的物料符合軌道運輸和貨架存儲的要求,同時保證倉庫管理系統(tǒng)中物料信息與實物一致。
倉儲管理
倉儲管理是物流系統(tǒng)中的另一重要環(huán)節(jié),是物流系統(tǒng)的調運中心。應用現代信息技術,針對物料的具體貯存條件對不同倉庫進行區(qū)域管理,合理高效地使用倉儲設施,可幫助企業(yè)極大提高制造物流系統(tǒng)的效率。
智能化的倉庫管理系統(tǒng)可實現對實體庫房的電子化管理,對物料信息、庫存信息、貨位信息進行可視化監(jiān)控。此外,系統(tǒng)可對庫存物料、貨位占用率、貨位承重、貨位使用頻次等數據進行實時統(tǒng)計和分析,為優(yōu)化庫房管理提供決策基礎,實現對庫房的高效利用。
除了通過合理的利用倉儲設施來提高庫房的利用效率以外,企業(yè)也可以通過端到端的供應鏈優(yōu)化,利用信息技術、管理手段,通過與原材料供應商合作,降低原材料、包材等的庫存水平,減少倉儲設施的占用?!傲銕齑妗边@一概念正是要求物料在采購、生產和配送環(huán)節(jié),不以倉儲的形式存在,而是處于周轉狀態(tài),降低企業(yè)庫存成本。通常包括了供應商管理的庫存(Vendor Managed Inventory,VMI)和準時制生產方式(Just In Time,JIT)等方式。這些方式利用端到端的供應鏈視角,通過和物料供應商的合作,建立信息的共享機制和平臺,設定庫存管理的合作性策略。綜合考慮生產計劃、物料質量控制和檢驗策略、物料生產周期和運輸周期,信息流和實物流優(yōu)化,與物料供應商一起設定最優(yōu)的庫存管理策略。
(摘編自《中國制藥工業(yè)智能制造白皮書(2020年版)》,工信部產業(yè)發(fā)展促進中心、中國醫(yī)藥企業(yè)管理協會聯合編制)